Continental‘s new white paper highlights nearly a century of tyre testing history at the company.
For Each New Model, Continental Conducts Tests Equivalent to Circling the Earth 625 Times
Premium tyres offer superior performance with shorter braking distances on wet and dry roads, quieter rolling noise, low rolling resistance, and long tread life. These are the results of rigorous testing during the development process and quality control.
Continental‘s tyre business division has detailed these procedures in the new “Tyre Testing White Paper,” which highlights nearly a century of tyre testing history at Continental. It also explores the evolution and application of current testing methods and provides a glimpse into the future of tyre testing.
Martin Welzhofer, Director of Global Tire Testing at Continental Tires, states in an official statement, “We conduct tests covering around 25 million kilometers annually with new tyre models. This distance is equivalent to circling the Earth 625 times. Extensive testing is essential to assess the performance of our tyres and ensure high quality and safety.”
Objective and Subjective Tire Tests: From Braking Performance to Rolling Noise
The document categorizes tyre tests into objective and subjective types. Objective tests include laboratory tests and extensive braking tests on wet, icy, snowy, and dry roads. Subjective tests involve driving tests to evaluate tyre performance on the road.
Professional drivers conduct these tests on Continental test tracks worldwide, analyzing vehicle stability and handling on various surfaces, during different seasons, on straight sections, curves, and at high speeds.
These tests also examine the rolling noise of the tyre. While a tyre may perform well in automated laboratory tests, it might produce annoying noises detectable only during actual driving. The white paper offers detailed information on both testing types and the factors influencing them.
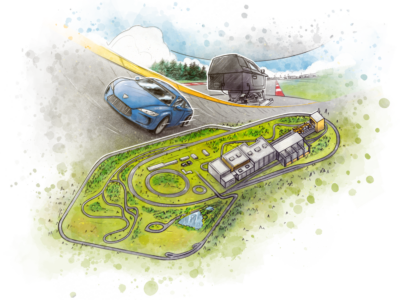
Virtual Testing: Saving Time and Resources
Digitalization has enabled more automated and virtual test procedures in tyre development. Continental initiated automation in 1968 with its first driverless test vehicle. Today, digital testing is crucial to the company’s tyre development.
A prime example is the driving simulator at the Contidrom test centre near Hannover, Germany. This driving-in-loop (DIL) simulator calculates the precise parameters of tyre driving dynamics and the corresponding test vehicle.
Its advanced movement capabilities provide test drivers with subjective driving experiences comparable to real test track conditions. These virtual methods allow Continental to tailor tyre solutions more efficiently and accurately to customer requirements, even before manufacturing the first tyre, thus saving time and resources.
Success Through Extensive Testing
Continental‘s tyres consistently top independent test lists due to rigorous testing. For instance, the seventh generation of the PremiumContact summer tyre line has impressed experts. In March, the Auto Club Europe (ACE) named the PremiumContact 7 the test winner for its shortest braking distances, impressive handling due to good grip, and balanced steering response across all driving types.
Achieving such performance requires precise and reproducible testing methods. The importance of extensive pre-production testing is also evident in the Continental UltraContact NXT, the most sustainable production tyre to date.
With up to 65% renewable, recycled, and mass balance-certified materials, the tyre boasts high sustainability. All 19 dimensions received the EU tyre label’s highest rating (“A”) for rolling resistance, wet braking, and external noise. The UltraContact NXT exemplifies how safety, performance, and sustainability can coexist seamlessly.